Getting deliveries to your consumer base is an important part of running an eCommerce site. While it may seem like this up to your shipping service, there are ways you can ensure your packages arrive on time. One way you can achieve fast distribution is through warehouse inventory management.
Warehouse inventory management involves the organisation, tracking, and control of goods within a warehouse. The goal is to minimise waste and maximise efficiency through proper planning.
Here’s how you can optimise your warehouse for both you and your consumer’s convenience.
Conduct Regular Inventory Audits and Cycle Counts
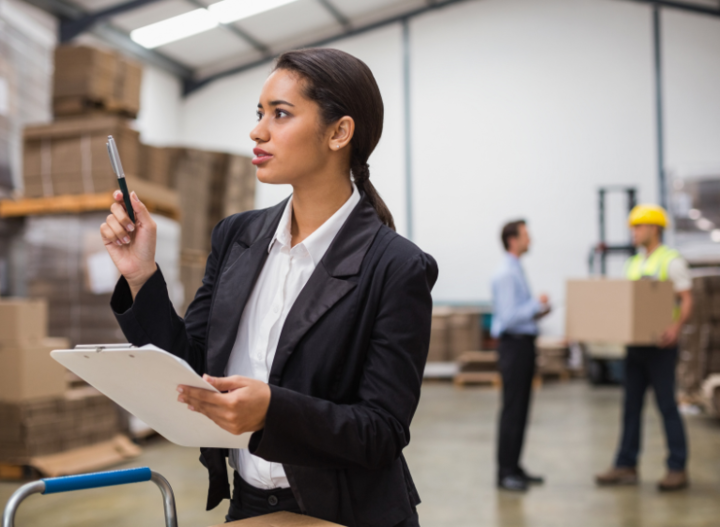
One of the easiest ways to optimise your warehouse is to know what’s in it. Inventory audits and cycle counts help business owners stay up-to-date with their stock.
An inventory audit is a comprehensive review of a business’s entire inventory. It typically involves physically counting all of the inventory items in the warehouse and comparing them to the records in the inventory management system.
A cycle count, on the other hand, is a more frequent, focused count of a specific group of inventory items. It typically involves counting a smaller selection of inventory items on a regular basis, such as once a week or once a month.
Businesses use cycle count to maintain accurate inventory records and identify discrepancies on a more frequent basis, rather than waiting for an annual inventory audit. However, both inventory audits and cycle counts will help you find any discrepancies in your warehouse.
Use Accurate Inventory Tracking Solutions
Tracking inventory enables companies to have a clear understanding of the quantity and location of their stock. It encompasses monitoring item levels and product movements in real-time
Doing this guarantees that products are available in the required places at the appropriate time. You will also reduce unnecessary expenditures and maximise productivity by detecting and rectifying inventory mistakes. This includes problems like overstocking or understocking a particular item based on trends.
Inventory tracking can be done in different ways, such as manually or by using technology like barcode scanning or RFID systems. Technologies like these enable companies to track inventory with speed and precision, thus increasing accuracy and lowering human errors.
Forecast and Strategically Plan Your Inventory
Proper planning and forecasting of inventory requires anticipating future inventory needs. By understanding your needs you can make necessary changes to avoid stockouts (a situation where an item is out of stock) and overstocking.
Through proper forecasting, you can make inventory decisions based on trends and easy-to-read displays. You’ll know when is the best time to reorder stock and the right amount to order. All of this leads to a more streamlined operation that doesn’t have you throwing money at slow-moving products.
Inventory planning and forecasting can be done by using technology such as inventory management software or automated forecasting systems such as enterprise resource planning software (ERP).
Read more about ERP and how it could help you better manage your warehouse.
Optimising Your Storage
Optimising storage involves utilising warehouse space to enhance storage capacity and minimise waste. This means knowing what to store together and efficiently placing products so no one is running back and forth around the warehouse trying to find the right item.
Effectively using every inch of space in the warehouse helps businesses to cut down costs and increase delivery times.
There are various methods that can be employed to optimise storage in a warehouse, such as:
Maximising Space: By identifying areas of the warehouse where space is being wasted and devising ways to utilise that space more effectively. Some ways you can accomplish this is through installing racking or shelving.
Consolidating Inventory: Combining multiple products into a single storage location to free up space and eliminate clutter.
Strategic Slotting: Analysing product demand and order patterns to determine the ideal location for each product within the warehouse to reduce searching for popular orders. .
Automated Storage Solutions: Using automated storage and retrieval systems (ASRS) to improve space utilisation and efficiency. ASRS i employs computer-controlled equipment to efficiently store and retrieve materials.
Cross-Docking: Receiving goods and immediately shipping them out to customers without storing them, which can reduce the need for warehouse space.
Utilise Barcode Scanning and RFID
In warehouse inventory management, barcode scanning and radio-frequency identification (RFID) technology are widely utilised to track inventory in real-time. These technologies enable businesses to find inventory with speed and precision, thus increasing accuracy and lowering human errors.
Barcode scanning has long been a popular method for all types of stores. Simply scan a barcode and your inventory software is updated.
On the other hand, RFID utilises radio waves to communicate between RFID tags and RFID readers. RFID tags are small, wireless chips that can be attached to products or inventory items, and RFID readers are used to read the data stored on the tags.
RFID technology allows for real-time tracking of inventory, as well as the ability to track multiple items at once, making it more efficient than barcode scanning.
Safety and Security Measures
Safety and security measures help to ensure that inventory is protected from theft, damage, and other hazards. They also protect employees from accidents and injuries.
Some examples of safety and security measures in warehouse inventory management include:
- Surveillance cameras
- Use of key cards or scanners to control who comes into the warehouse
- Alarm systems
- Installing proper lightingFire suppression systems such as fire extinguishers and sprinklers
- Devising emergency response plans
- Proper employee safety training
Understand Inventory Reorder Points and Reorder Quantity
Reorder point and reorder quantity are important processes in warehouse inventory management. Automating these optimises your entire warehouse operation and helps you avoid stockouts and lost sales.
Reorder point considers a few factors such as production times, how much inventory you use, and the right level of safety stock in case a particular item sells out faster than usual.
When a warehouse reaches the level at which it needs to reorder a particular product, it will order the calculated quantity . This ensures that the company always maintains the appropriate amount of inventory to fulfil customer needs.
Manage Your Supply Chain
Supply chain management involves the flow of goods in an efficient manner. It requires sourcing goods transferring them from the manufacturer or supplier, and the eventual distribution of the materials to the end consumer.
Quality control is an important aspect of managing your supply chain. Quality control makes sure that the items procured are in good condition and are fit to be delivered to the consumer.
At the top of proper supply chain management is relationship management. Managing your relationships with both your supplier and consumers ensures everyone is happy with your business and services.